āA huge bottleneck exists in terms of time wasted in harvesting and threshing that is preventing timely sowing of crops,ā said Scott Justice, agriculture mechanization specialist, CIMMYT. The Cereal Systems Initiative for South Asia (CSISA) is working to ensure smallholder farmers have access to machinery based on their specific requirements by improving existing designs to meet local needs.”
For shelling maize, farmers in Bihar can either purchase a very large, efficient machine that costs approximately US $786 or use a cheap handheld sheller that can shell only 15-20 kilograms per hour. According to Justice, āthese lightweight, affordable shellers are relatively new on the scene. Their simple design means that they can easily be made by local manufacturers and can also be modified as required.ā
CSISA worked with a local manufacturer to modify the design of a medium-sized sheller and created a double cob maize sheller powered by an electric motor, which can shell 150 kg of maize per hour and consumes only 2-4 units of electricity. Priced at US $126, the machine is fairly affordable. āIn fact, half the cost of the machine is that of the electric motor alone. For farmers who already own one, the machine would only cost US $63,ā said Suryakanta Khandai, Postharvest Specialist at the International Rice Research Institute (IRRI), who works for CSISA in Bihar.
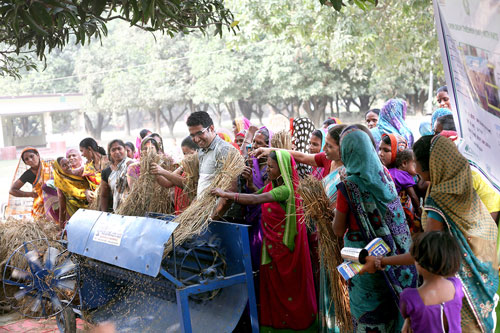
Photo: CSISA
Until recently, farmers in Bihar only had two options for mechanized rice threshing āa very large axial flow thresher that can cost up to US $2,700 with subsidies, or a pedal-powered, open-drum thresher that has very low capacity and is difficult to operate for extended periods.
āFarmers clearly needed a medium-sized, affordable, efficient and portable mechanical rice thresher,ā said Khandai. āThe existing models lacked grain-separating or bagging functions, which we included in the new design. In addition to giving it wheels, we also decided to use a diesel engine to power the machine to allow for threshing in the field immediately upon cutting, which helps reduce losses.ā The result was a diesel-powered, open-drum thresher.
It costs US $23.96 to hire one person to manually thresh one acre of rice and it takes seven days. However, the diesel-powered, open-drum thresher covers the same area in just over four hours, at a total cost of US $10.54.
Since the modified machines do not offer an attractive profit for larger manufacturers and retailers, CSISA approached local companies to fill the gap. The maize sheller was customized in cooperation with Dashmesh Engineering, which sells the machine at a profit of US $11ā13. āProfits help ensure that the manufacturers are motivated to scale out the machines,ā said Khandai.
Justice added, āEquipment like the diesel-powered, open-drum rice thresher is very simple but has not spread very widely. I feel these should now also be promoted to the owners of two-wheel tractors and mini tillers in India and Nepal.ā